The last major technological innovation in fire-rated glazing was the development of fire-resistive intumescent glazing in the 1980s. A revolutionary development at the time, it consisted of thin layers of a transparent intumescent interlayer sandwiched between pieces of tempered or annealed glass. When exposed to the heat of fire, the interlayers chemically react to form opaque, insulating layers. These layers prevent the spread of smoke and flame as well as the transfer of radiant heat.
Because the heat will eventually degrade the intumescent interlayer, higher minute ratings are achieved by adding more layers of glass and interlayers, with each successive layer holding back the heat, smoke, and flame. Thus, a 120-minute partition assembly can be 1.5x to 2x as thick as a 60-minute partition.
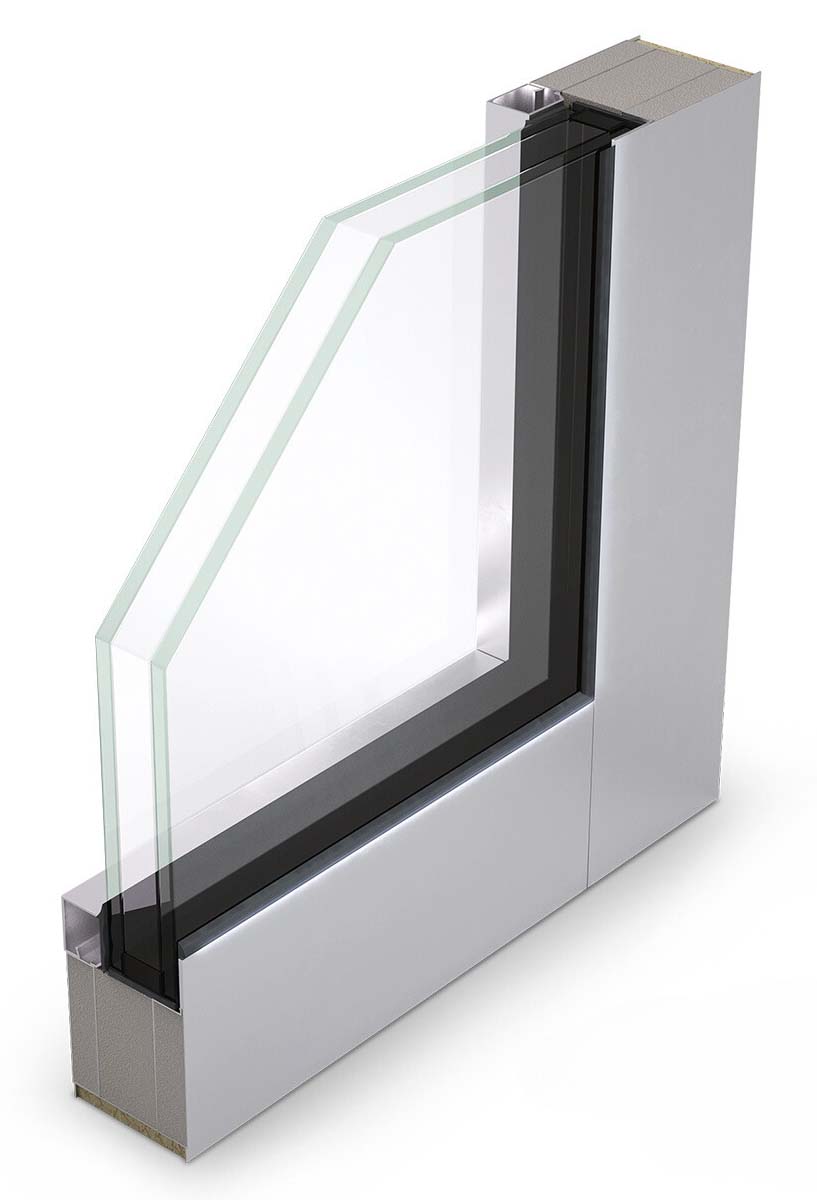
The first fire-rated glass to feature a single-chamber foaming interlayer for all performance ratings, CONTRAFLAM® One is clearer, thinner, lighter, and more sustainable. Click to enlarge
This technology, as applied in previous generations of Vetrotech’s CONTRAFLAM products, has served the industry well for decades. However, the additive process for increasing performance ratings comes at a cost beyond thicker assemblies, including:
- Reduced clarity
- Heavier weight
- Smaller areas between frames
- Increased raw material use
CONTRAFLAM® One changes the equation completely. It is the first and only fire-resistive glazing solution that requires a single intumescent chamber and two pieces of glass for all performance ratings. That means both the 60-minute partition and the 120-minute partition consist of two pieces of glass and one chamber. The innovation is due to new Hybridcore™ technology, the result of Vetrotech’s four decades of experience in interlayer chemistry.
This groundbreaking interlayer technology is revolutionizing fire-resistive glazing in three key ways:
1. Greater Design Freedom
As it delivers outstanding fire-rated capabilities, CONTRAFLAM One’s impressive light transmission values and thinner makeups empower architects with greater design freedom. Traditional multilayer fire-resistive glass can lose as much as 13% VLT between 60-minute and 120-minute products, while CONTRFLAM One 120-minute maintains 89% VLT—the highest available. It also features the largest maximum area uninterrupted by framing: 44.9 ft2 at 120 minutes, compared to an average of 30.1 ft2 among competitive products.
CONTRAFLAM One can be specified for any application where architectural glass is found: interior partitions, exterior windows and walls, flooring, and more. Additional features available for CONTRAFLAM One assemblies include impact protection for added safety, double- and triple-glazing for energy savings, extra clear options, and extra privacy and noise reduction for occupant comfort. CONTRAFLAM One lets architects take full advantage of all the design benefits of glass while ensuring safety, comfort, and sustainability.
2. Less Stress on the Construction Team
Across the AEC industry, “do more with less” has gone from mindset to reality. Nowhere is that more true than in construction labor. From roofing to flooring installation, carpentry to plumbing, no trade is immune to the epidemic of skilled labor shortage─including glaziers.
CONTRAFLAM One’s innovative construction makes transportation, handling, and installation infinitely easier for glazing subcontractors. Weighing up to 31% less than competitors, it is the lightest fire-resistive glass product on the market. CONTRAFLAM One also uses tempered glass for added strength and is resistant to temperatures ranging from -40°F to +140°F, providing stability contractors can rely on from factory to installation. The combination of these elements results in worry-free transportation, ease of handling, and measurably faster installation.
Maintaining your design vision and avoiding pushback on specs becomes much easier when you specify products that benefit the subcontractors as much as the design.
3. Dramatic Reduction in Embodied Carbon
Sustainability is part of Vetrotech’s DNA, and any product innovation introduced to the marketplace must further the cause of reducing the built environment’s impact on our global climate. CONTRAFLAM One was developed to help architects design more sustainably, with up to 35% less embodied carbon than multi-chamber products.
Embodied carbon represents carbon emissions released during the life cycle of a building material, from the extraction of the raw materials needed to produce it to the processing and disposal of waste at the end of its useful life. Between 65% and 85% of total embodied carbon emissions are produced during the product phase─raw material acquisition, supply and transport, and manufacturing. Requiring less glass to manufacture significantly reduces the embodied carbon.
CONTRAFLAM One has demonstrated higher levels of stability than conventional fire-resistive glazing, thus extending the life of the product. Owners can reduce the use of replacement glass materials and dispose of fewer lites of glass over the course of a building’s life cycle. And when the time comes for disposal, CONTRAFLAM One delivers yet another advantage. The Hybridcore Technology that makes the single-chamber composition possible contains no carcinogenic or otherwise hazardous materials that would be released into the environment.
When CONTRAFLAM One is paired with Vetrotech’s VDS framing system, the two form a line of code-compliant, fire-rated assemblies manufactured in the U.S., complete with EPD and HPD documentation for maximum transparency. VDS is the only fire-rated framing system with third-party verified EPDs and HPDs.
By Michael Miller, Assoc. AIA, North America Sales Manager, Vetrotech Saint-Gobain
Michael Miller has more than a decade of expertise in fire-rated glazing. His background spans commercial construction, real estate development, technology startups, and government, and he holds degrees in Architecture and Political Science from Ball State University.
Post a comment to this article
Report Abusive Comment